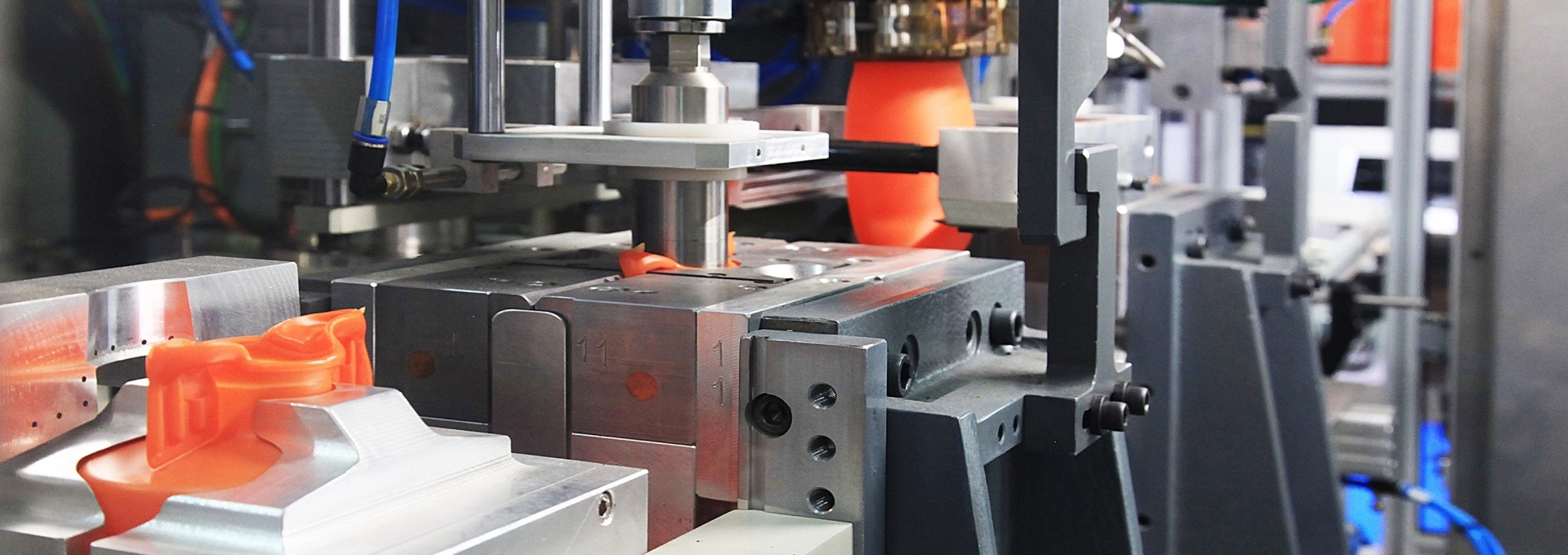
L’injection plastique s’est imposée comme une technologie de fabrication révolutionnaire, transformant radicalement les processus de production dans de nombreux secteurs industriels. Cette méthode, alliant précision, rapidité et polyvalence, permet de concevoir des pièces complexes tout en optimisant les coûts et les délais de fabrication. Son impact sur l’industrie moderne est tel qu’elle est devenue un pilier incontournable pour les entreprises cherchant à rester compétitives sur un marché en constante évolution.
Principe et fonctionnement de l’injection plastique
L’injection plastique repose sur un principe relativement simple mais ingénieux. Le processus débute par la fusion de granulés de plastique, généralement des thermoplastiques, dans un cylindre chauffé. Cette matière fondue est ensuite injectée sous haute pression dans un moule spécialement conçu pour la pièce à produire. Une fois le plastique refroidi et solidifié, le moule s’ouvre pour éjecter la pièce finie.
La clé de l’efficacité de ce procédé réside dans la précision du contrôle de chaque paramètre. La température, la pression et la vitesse d’injection sont minutieusement réglées pour garantir la qualité optimale du produit final. Les machines d’injection modernes sont équipées de systèmes de contrôle sophistiqués permettant une maîtrise totale du processus, réduisant ainsi les risques de défauts et assurant une reproductibilité exceptionnelle.
Le choix du matériau plastique est crucial et dépend des propriétés requises pour la pièce finale. Des polymères tels que le polyéthylène, le polypropylène, l’ABS ou le polycarbonate sont couramment utilisés, chacun offrant des caractéristiques spécifiques en termes de résistance, de flexibilité ou de résistance thermique.
Avantages techniques de l’injection plastique dans l’industrie
L’injection plastique présente de nombreux avantages techniques qui expliquent son adoption massive dans l’industrie. Sa capacité à produire des pièces complexes avec une grande précision, tout en maintenant des cadences de production élevées, en fait une solution particulièrement attractive pour de nombreux secteurs.
Précision dimensionnelle avec la technologie de moule à canaux chauds
L’une des innovations majeures dans le domaine de l’injection plastique est l’utilisation de moules à canaux chauds. Cette technologie permet d’obtenir une précision dimensionnelle exceptionnelle, cruciale pour la production de pièces techniques aux tolérances serrées. Les canaux chauds maintiennent le plastique à l’état fondu jusqu’au point d’injection, réduisant ainsi les défauts liés au refroidissement prématuré de la matière.
La précision obtenue grâce à cette technique est telle qu’elle permet de produire des composants micro-mécaniques pour l’industrie horlogère ou des pièces médicales aux tolérances de l’ordre du micron. Cette exactitude dimensionnelle est particulièrement appréciée dans les secteurs où la fiabilité et la reproductibilité sont essentielles.
Flexibilité des matériaux : du PVC au PEEK
L’injection plastique offre une flexibilité remarquable en termes de choix de matériaux. Du PVC, économique et polyvalent, au PEEK, un polymère haute performance résistant à des températures extrêmes, la gamme de matériaux disponibles est vaste. Cette diversité permet aux concepteurs de sélectionner le matériau idéal pour chaque application, qu’il s’agisse de résistance chimique, de propriétés mécaniques ou de caractéristiques thermiques spécifiques.
Par exemple, le polyétheréthercétone (PEEK) est de plus en plus utilisé dans l’aérospatiale pour remplacer certaines pièces métalliques, offrant une réduction de poids significative sans compromis sur la résistance. À l’autre extrémité du spectre, des bioplastiques biodégradables sont désormais injectables, répondant aux préoccupations environnementales croissantes.
Réduction des coûts par la production en grande série
L’un des avantages économiques majeurs de l’injection plastique est sa capacité à produire en grande série à des coûts unitaires très compétitifs. Une fois le moule conçu et fabriqué, le coût de production par pièce diminue considérablement avec l’augmentation du volume de production. Cette économie d’échelle rend l’injection plastique particulièrement attractive pour les industries nécessitant de grandes quantités de pièces identiques.
De plus, l’automatisation poussée des lignes de production d’injection plastique permet de réduire les coûts de main-d’œuvre tout en maintenant une qualité constante. Les systèmes de contrôle qualité intégrés assurent une détection précoce des défauts, minimisant ainsi les rebuts et optimisant l’utilisation des matières premières.
Optimisation du cycle d’injection avec les presses électriques
L’avènement des presses à injection électriques a marqué un tournant dans l’optimisation du cycle d’injection. Contrairement aux presses hydrauliques traditionnelles, les presses électriques offrent un contrôle plus précis des mouvements, une consommation énergétique réduite et des cycles plus rapides. La précision accrue des mouvements permet d’obtenir des pièces de meilleure qualité avec des temps de cycle réduits.
Les presses électriques sont particulièrement efficaces pour la production de pièces techniques nécessitant un contrôle strict des paramètres d’injection. Leur flexibilité permet des ajustements rapides des paramètres de production, réduisant ainsi les temps de configuration entre les différentes séries de production.
Applications sectorielles de l’injection plastique
L’injection plastique trouve des applications dans une multitude de secteurs industriels, chacun exploitant ses avantages spécifiques pour répondre à des besoins particuliers. De l’automobile à l’aérospatiale, en passant par le médical et l’électronique, cette technologie s’est imposée comme une solution de fabrication incontournable.
Automobile : pièces légères pour réduire la consommation
Dans l’industrie automobile, l’injection plastique joue un rôle crucial dans la réduction du poids des véhicules, un facteur clé pour améliorer l’efficacité énergétique et réduire les émissions de CO2. Des composants tels que les tableaux de bord, les pare-chocs, les réservoirs de carburant et même certaines pièces du moteur sont désormais fabriqués en plastique injecté.
L’utilisation de plastiques renforcés de fibres permet de remplacer certaines pièces métalliques par des équivalents en plastique plus légers tout en conservant les propriétés mécaniques nécessaires. Cette substitution peut entraîner une réduction de poids allant jusqu’à 50% pour certains composants, contribuant significativement à l’allègement global du véhicule.
Médical : dispositifs stériles à usage unique
Le secteur médical bénéficie grandement de la précision et de la stérilité offertes par l’injection plastique. La production de dispositifs médicaux à usage unique, tels que les seringues, les cathéters ou les implants, requiert des normes de qualité et d’hygiène extrêmement élevées. L’injection plastique permet de répondre à ces exigences tout en assurant une production en grande série économiquement viable.
Les plastiques biocompatibles utilisés dans ce secteur, comme le polyéthylène haute densité (PEHD) ou le polypropylène (PP), garantissent la sécurité des patients tout en offrant les propriétés mécaniques nécessaires pour des applications médicales spécifiques. La possibilité de produire des formes complexes en une seule opération réduit également les risques de contamination liés aux assemblages multiples.
Électronique : boîtiers résistants aux chocs
L’industrie électronique fait largement appel à l’injection plastique pour la fabrication de boîtiers et de composants. Les plastiques techniques utilisés dans ce secteur offrent une combinaison unique de propriétés : légèreté, résistance aux chocs, isolation électrique et dissipation thermique.
Des matériaux comme l’ acrylonitrile butadiène styrène (ABS) ou le polycarbonate (PC) sont couramment utilisés pour produire des boîtiers d’appareils électroniques résistants aux chocs et aux rayures. L’injection plastique permet également d’intégrer directement des fonctionnalités telles que des clips de fixation ou des guides de câbles, simplifiant ainsi l’assemblage et réduisant les coûts de production.
Aérospatiale : composants complexes allégés
Dans le secteur aérospatial, où chaque gramme compte, l’injection plastique offre des solutions innovantes pour réduire le poids des composants tout en maintenant leurs performances. Des pièces structurelles complexes, auparavant usinées en métal, sont désormais produites en plastiques haute performance comme le PEEK ou le polyétherimide (PEI).
Ces matériaux offrent une résistance exceptionnelle aux températures extrêmes et aux produits chimiques, tout en étant significativement plus légers que leurs équivalents métalliques. L’injection plastique permet de produire ces pièces avec une précision dimensionnelle élevée, essentielle dans un domaine où la sécurité et la fiabilité sont primordiales.
Innovations technologiques en injection plastique
Le domaine de l’injection plastique est en constante évolution, avec des innovations technologiques qui repoussent sans cesse les limites de ce qui est possible. Ces avancées permettent de produire des pièces toujours plus complexes, plus performantes et plus économiques.
Moulage par injection assistée par gaz (GAIM)
Le moulage par injection assistée par gaz (GAIM) est une technique innovante qui permet de créer des pièces creuses ou partiellement creuses. Cette méthode consiste à injecter du gaz (généralement de l’azote) dans la cavité du moule immédiatement après l’injection du plastique fondu. Le gaz pousse le plastique contre les parois du moule, créant ainsi une structure creuse à l’intérieur de la pièce.
Cette technique offre plusieurs avantages :
- Réduction du poids des pièces sans compromettre leur rigidité
- Diminution du temps de cycle et de la consommation de matière
- Possibilité de créer des pièces complexes avec des sections variables
- Amélioration de l’aspect de surface des pièces
Le GAIM est particulièrement apprécié dans l’industrie automobile pour la production de pièces telles que les poignées de porte ou les conduits d’air, où la légèreté et la rigidité sont essentielles.
Injection multi-matières pour pièces complexes
L’injection multi-matières représente une avancée significative dans la production de pièces complexes. Cette technique permet de combiner différents matériaux ou couleurs en une seule opération de moulage, éliminant ainsi le besoin d’assemblages ultérieurs. Le processus implique l’utilisation de plusieurs unités d’injection qui injectent séquentiellement ou simultanément différents matériaux dans le moule.
Les applications de cette technologie sont vastes :
- Création de pièces bi-matières alliant rigidité et souplesse
- Intégration de joints d’étanchéité directement lors du moulage
- Fabrication de pièces esthétiques avec des combinaisons de couleurs complexes
- Production de composants électroniques avec des parties conductrices et isolantes
L’injection multi-matières ouvre de nouvelles possibilités en termes de design et de fonctionnalité, tout en simplifiant les processus de production et en réduisant les coûts d’assemblage.
Impression 3D des moules pour prototypage rapide
L’impression 3D révolutionne la fabrication des moules d’injection plastique, en particulier pour le prototypage rapide et les petites séries. Cette technologie permet de créer des moules complexes en quelques heures, contre plusieurs semaines pour les méthodes traditionnelles d’usinage.
Les avantages de l’impression 3D des moules sont nombreux :
- Réduction drastique des délais de développement
- Diminution des coûts pour les petites séries ou les prototypes
- Possibilité de tester rapidement différentes itérations de design
- Fabrication de géométries complexes difficiles à usiner conventionnellement
Bien que les moules imprimés en 3D ne soient généralement pas adaptés à la production de grandes séries, ils offrent une flexibilité incomparable pour les phases de développement et de validation de produits.
Enjeux environnementaux et solutions durables
Face aux préoccupations environnementales croissantes, l’industrie de l’injection plastique s’adapte en développant des solutions plus durables. Ces innovations visent à réduire l’impact environnemental tout en maintenant les avantages techniques et économiques du procédé.
Utilisation de bioplastiques et matériaux recyclés
L’intégration de bioplastiques et de matériaux recyclés dans les processus d’injection plastique représente une avancée majeure vers une production plus écologique. Les bioplastiques, dérivés de ressources renouvelables comme l’amidon de maïs ou la canne à sucre, offrent une alternative prometteuse aux plastiques conventionnels issus du pétrole.
Parallèlement, l’utilisation croissante de plastiques recyclés permet de réduire la consommation de matières premières vierges et de limiter les déchets. Les progrès réalisés dans les technologies de tri et de retraitement des plastiques permettent aujourd’hui d’obtenir des matériaux recyclés de haute qualité, compatibles avec les exigences techniques de nombreuses applications industrielles.
L’utilisation de ces matériaux alternatifs présente plusieurs avantages :
- Réduction de l’empreinte carbone de la production
- Diminution de la dépendance aux ressources fossiles
- Amélioration de l’image de marque des entreprises
- Conformité aux réglementations environnementales de plus en plus strictes
Cependant, l’intégration de ces matériaux dans les processus d’injection plastique nécessite souvent des ajustements techniques et une expertise spécifique pour maintenir les performances et la qualité des pièces produites.
Optimisation énergétique des presses d’injection
L’efficacité énergétique est devenue un enjeu majeur pour les fabricants de presses à injecter et les transformateurs de plastique. Les nouvelles générations de presses intègrent des technologies avancées visant à réduire significativement leur consommation d’énergie.
Parmi les innovations les plus marquantes, on peut citer :
- L’utilisation de moteurs électriques à haut rendement
- Les systèmes de récupération d’énergie lors des phases de freinage
- L’optimisation des circuits hydrauliques pour minimiser les pertes
- L’isolation thermique renforcée des cylindres de plastification
Ces améliorations techniques permettent non seulement de réduire la facture énergétique des entreprises, mais aussi de diminuer leur impact environnemental. Certaines presses modernes affichent des réductions de consommation d’énergie allant jusqu’à 50% par rapport aux modèles précédents.
Recyclage en boucle fermée des rebuts de production
La mise en place de systèmes de recyclage en boucle fermée représente une approche innovante pour réduire l’impact environnemental de l’injection plastique. Ces systèmes visent à réintégrer directement les déchets de production (carottes, pièces non conformes) dans le processus de fabrication, limitant ainsi le besoin en matière première vierge.
Le recyclage en boucle fermée présente plusieurs avantages :
- Réduction des coûts de matière première
- Diminution du volume de déchets envoyés en décharge
- Amélioration de l’efficacité globale du processus de production
- Réduction de l’empreinte carbone de l’entreprise
Certaines entreprises vont encore plus loin en développant des partenariats avec leurs clients pour la récupération et le recyclage des produits en fin de vie. Cette approche d’économie circulaire permet non seulement de réduire l’empreinte environnementale de l’industrie, mais aussi de créer de nouvelles opportunités économiques dans le domaine du recyclage et de la valorisation des matériaux.